Applications
Application of Inconel, Cobalt and Beryllium Copper
Superalloys, including Inconel, Hastelloy, Monel, Cobalt and Beryllium Copper, exhibit extraordinary properties: high strength, high wear resistance, high-temp stability or extreme corrosion resistance, and are mainly used in critical operating environments in petrochemical, marine and power plant industries. Typicl superalloys are:
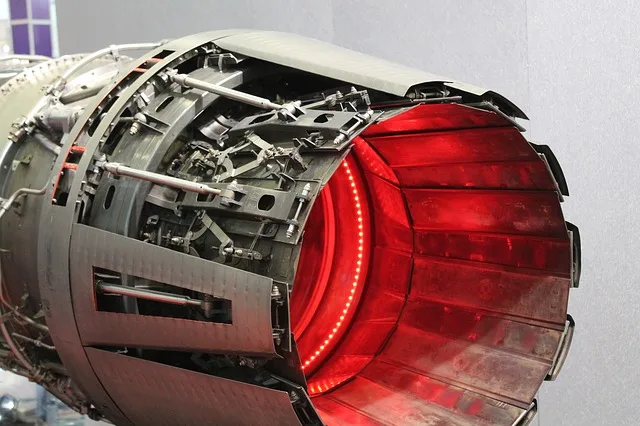
Aerospace
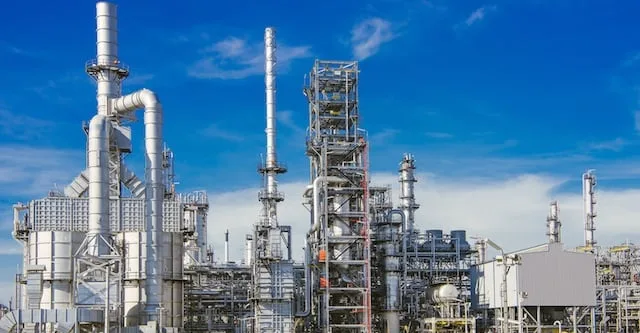
Petro Chemical
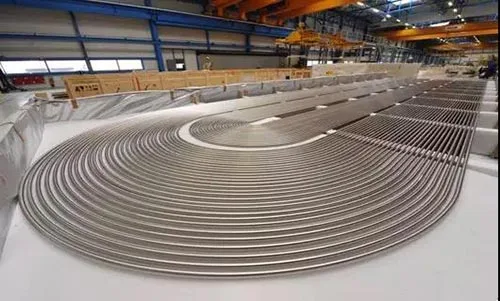
Power Generation
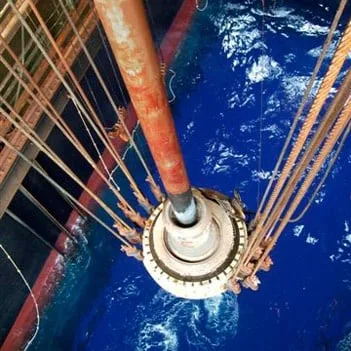
Marine
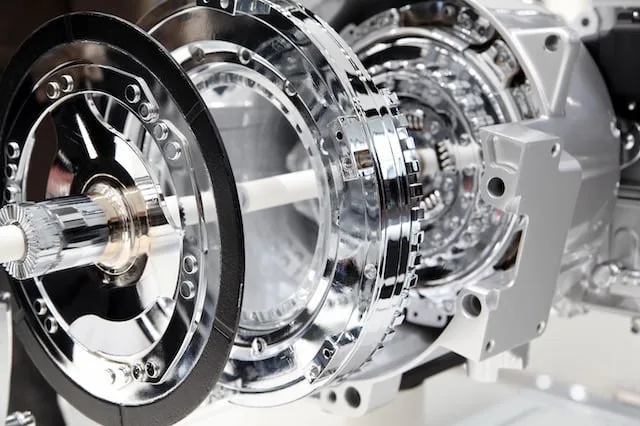
Automotive
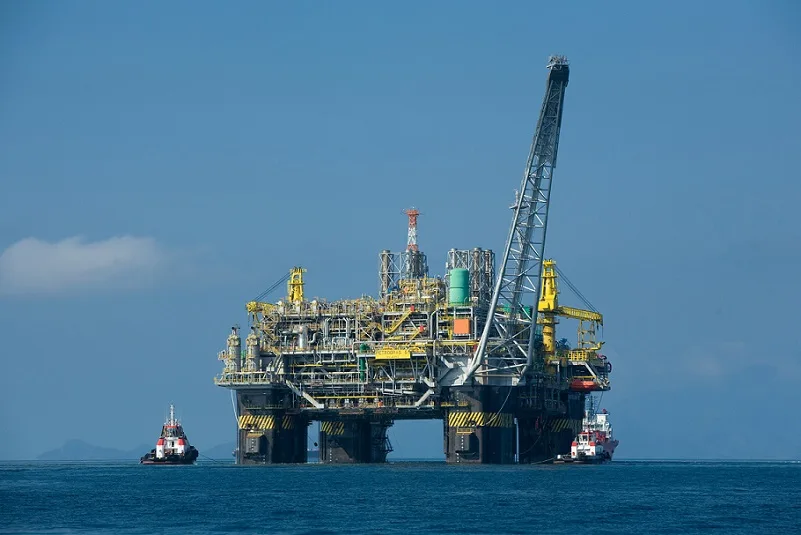
Oil & Gas
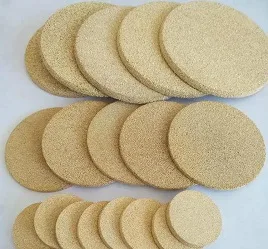
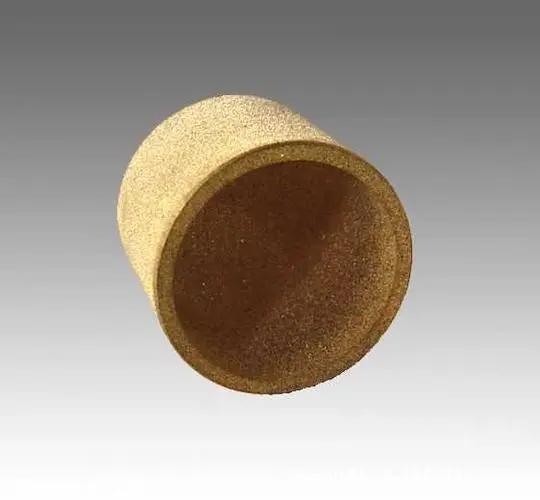
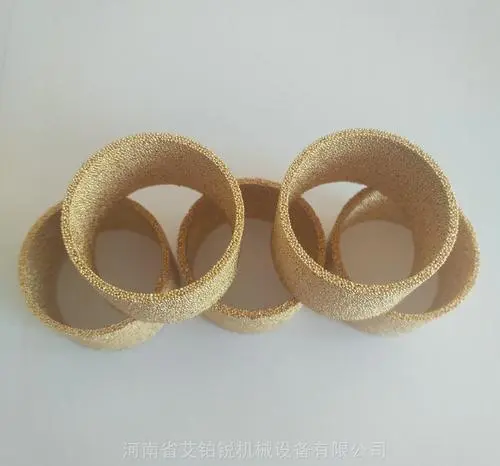
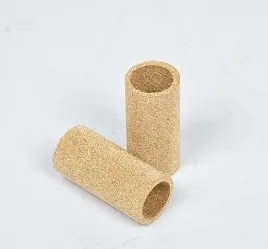
What is Sintered Filter?
Sintering gives the high porosity material its shape-stability and properties of a strong metal Component. Sintered Bronze product has a unique structure shows that the grain boundaries run over the original particle boundaries. The pores after the sintering process are mechanically fixed with respect to both size and position. Porosity, size and shape are the determining factor In producing sintered bronze product.
main applications of Sintered Filter
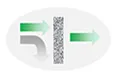
Filter
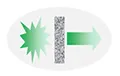
Sound Dampen
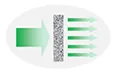
Heat Transfer
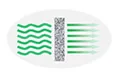